Glossar
0-9
3-Achs-Fräsen
Detaillierte Informationen finden Sie auf unserer Seite:
https://fraesen-online.de/Leistungen/3-achs-fraesen/
4-Achs-Fräsen
5-Achs-Fräsen – Angestellt und Synchron
Detaillierte Informationen finden Sie auf unserer Seite:
https://fraesen-online.de/Leistungen/5-achs-fraesen/
A
Aufkohlen
Abnahmeprüfzeugnis (Kontext Material):
den entsprechenden Glossareintrag finden Sie [hier].
Verwandte Glossareinträge:
2.1 – Werksbescheinigung / 2.2 – Werkszeugnis / 3.1 – Abnahmeprüfzeugnis / FDA Zulassung
B
Build-to-Print
Fertigung nach Zeichnung. Alle Rahmenbedingungen sollten geklärt sein. Es ist eher keine Rücksprache gewünscht.
Brünieren
Brünieren ist eine relativ kostengünstige Oberflächenbehandlung für Stahlwerkstoffe und dient als dekorativer Korrosionsschutz.
- Aluminium brünieren
Brünieren bezeichnet einen Prozess, der für Aluminiumwerkstoffe nicht geeignet ist. Soll ein Aluminiumbauteil eine schwarze Oberfläche erhalten, kann es schnell und relativ kostengünstig eloxiert werden. Beim Eloxieren steht die dekorative Eigenschaft im Vordergrund. Zusätzlich erhöht die Eloxalschicht den elektrischen Widerstand erheblich und kann als Verschleißschutz eingesetzt werden (Harteloxal). - Edelstahl brünieren
Umgangssprachlich wird das Brünieren manchmal als ‚Edelrost‘ bezeichnet. Dies veranschaulicht treffend, dass beim Brünieren die Oberfläche oxidiert und eingefärbt wird. Aus diesem Grund können nichtrostende Stähle nicht brüniert werden. Je nach Legierung ist es möglich, dass das Werkstück eine gelbliche Färbung erhält. Die verfahrenstypische schwarze Oberfläche wird nicht erreicht.
D
Diffundieren
Distributed Numerical Control (DNC)
Mit einer DNC-Verbindung können Werkzeugmaschinen mit Computern verbunden werden. Dies ermöglicht eine Datenübertragung in oder aus einem Lokales Netzwerk (LAN).
Drehen
Drehzahlberechnung beim Fräsen
Formeln zur Drehzahlberechnung beim Fräsen finden Sie [hier]
E
Edelstähle
Edelstähle können vier Gruppen eingeteilt werden.
- Austenitische Edelstähle
Eigenschaften: eher nicht magnetisch
z.B.: 1.4301 - Ferritische Edelstähle
Eigenschaften: eher magnetisch - Martensitische Edelstähle
Eigenschaft: sind härtbar, eher nicht magnetisch
1.4057 – kann z.B. Vorvergütet auf 265 HB bezogen werden - Duplexstähle
Eingriffsbreite ae:
Die Eingriffsbreite ae bezeichnet die seitliche Zustellung des Fräswerkzeuges und wird rechtwinklig zur Vorschubrichtung bestimmt.
Sowohl die Eingriffsbreite ae als auch die Schnitttiefe ap hängen vom Werkzeugtyp und dem Material des Werkstücks ab. Für spezifische Einsatzwerte kann man sich auf Tabellen der Werkzeughersteller beziehen.
Die richtige Einstellung dieser Parameter hat direkte Auswirkungen auf die Belastung und den Verschleiß des Werkzeugs. Durch die Optimierung der Eingriffsbreite und Schnitttiefe können nicht nur die Lebensdauer des Werkzeugs verlängert und die Bearbeitungszeit verkürzt werden, sondern auch die Qualität der bearbeiteten Oberfläche und die Maßhaltigkeit verbessert werden. Zudem führt dies zu einem stabileren Fräsprozess.
ap und ae bei einem Schaftfräser:
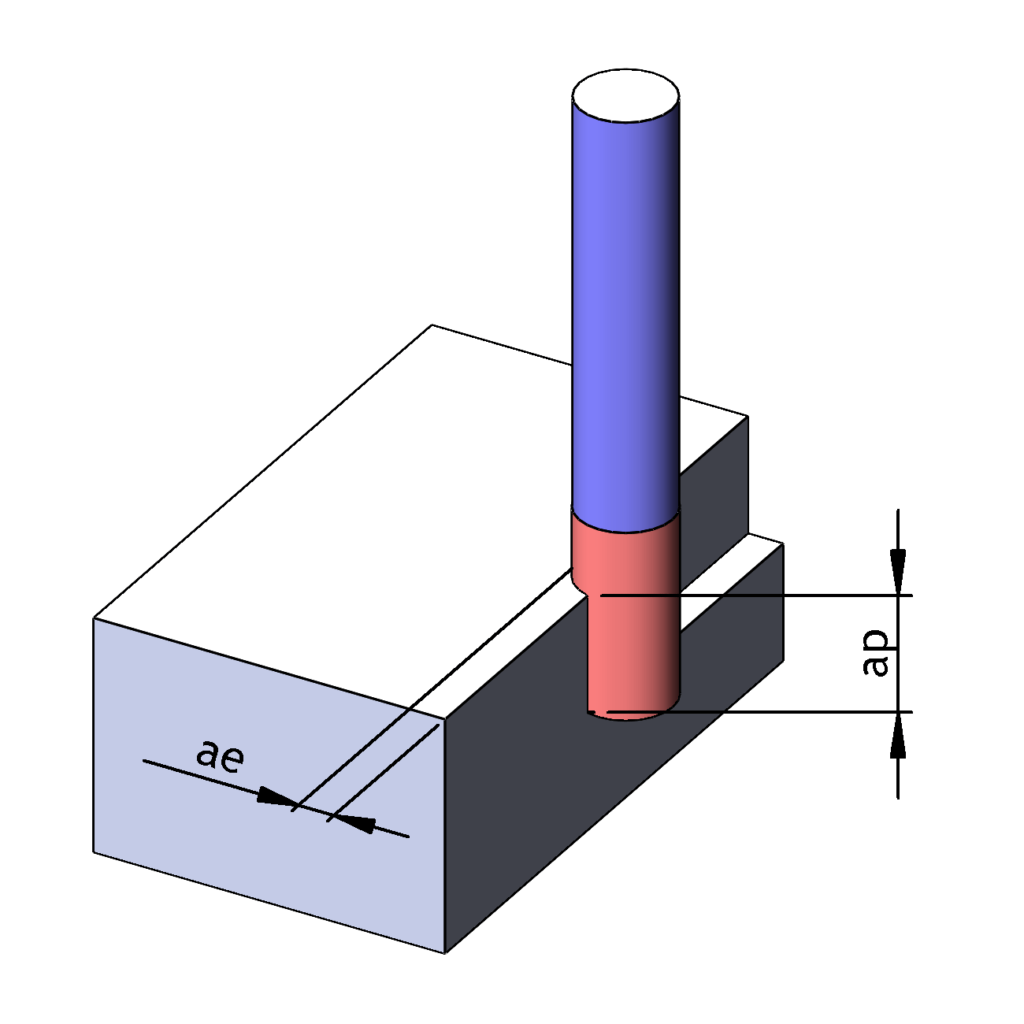
ap und ae bei einem Messerkopf:
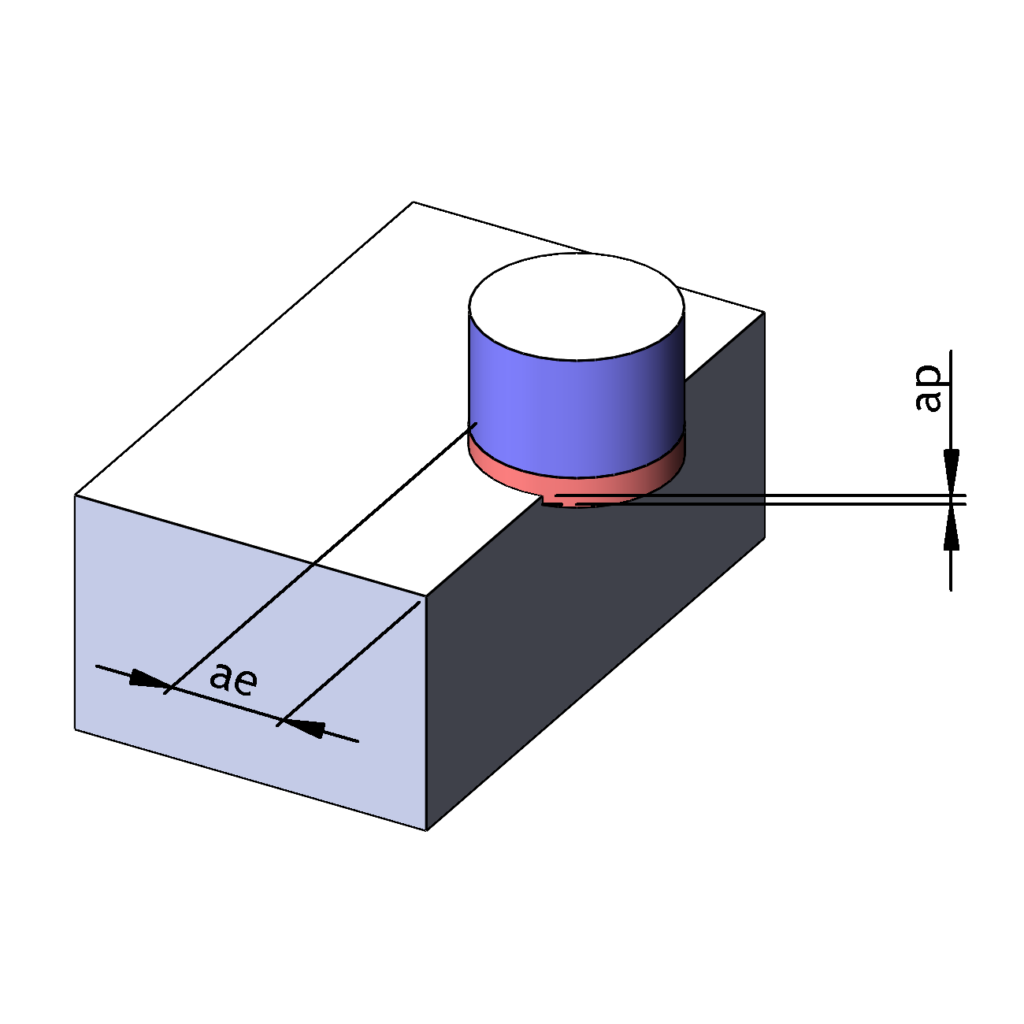
Verwandte Glossareinträge:
Eingriffsbreite ae / Formeln Fräsen ff./ Schnittgrößen / Schnitttiefe ap
Einsatzhärten
Elektrisch nicht optimierte Kunststoffe
elektrisch nicht optimierte Kunststoffe, können als elektrisch nicht Leitfähig bezeichnet werden. Der elektrischen Widerstand befindet sich in einem Bereich zwischen 10^12 und 10^14 Ohm.
Elektrisch aktive Kunststoffe
Ein Hauptanwendungsfall für diese Materialgruppe sind Bauteile um sensible elektronische Komponenten. In Verbindung mit einer Erdung kann so eine anliegende Spannungen abgeleitet werden um Schäden zu vermieden. Über den Wiederstand des Material kann Einfluss auf die Entladezeit genommen werden.
- AST Kunststoffe / AS Kunststoffe / ESD Kunststoffe
Zu dieser Materialgruppe werden Kunststoffe zugeordnet, welche einen elektrischen Widerstand zwischen 10^6 und 10^12 Ohm aufweisen.
Diese Gruppe wird auch als ESD-Kunststoffe oder ESD fähige Kunststoffe bezeichnet.
Wobei ESD (Electrostatic Discharge) für elektrostatische Entladung steht und AST oder AS für Antistatisch.
- ELS Kunststoffe / EL Kunststoffe
Als ELS oder Elektrisch leitfähig werden Kunststoffe bezeichnet, die einen elektrischen Widerstand zwischen 10^2 und 10^6 Ohm aufweisen.
Metalle
Wird ein elektrischer Widerstand kleiner 10^2 benötigt können Metalle verwendet werden.
Eloxieren
Erodieren
F
FDA Zulassung (Kontext Material):
den entsprechenden Glossareintrag finden Sie [hier].
Verwandte Glossareinträge:
2.1 – Werksbescheinigung / 2.2 – Werkszeugnis / 3.1 – Abnahmeprüfzeugnis / FDA Zulassung
Flammhärten
.
Fräsen
Durch das Fertigungsverfahren Fräsen werden ebene Flächen und Konturen, Abgesetzte Flächen und Konturen oder Freiformflächen hergestellt. Dabei wird ein rotierendes Werkzeug mit definierter Schneidenzahl durch das Werkstück bewegt. Bei einer Umdrehung des Fräswerkzeuges tritt jede Schneide in das Material ein, schält Material ab und tritt dann aus dem Material aus. Entgegen dem Drehen handelt es sich hier um einen unterbrochenen Schnitt, da die Schneiden nicht permanent Material abtragen. Dies hat eine erhöhte Beanspruchung von Werkzeug und Maschine zur Folge.
Weitere Informationen finden Sie auf unseren Seiten 3-Achs-Fräsen und 5-Achs-Fräsen.
Formeln – Häufig verwendete Formeln beim Fräsen
Formel | Normalform | Umgestellt 1 | Umgestellt 2 | Umgestellt 3 |
Drehzahl | n = (vc*1000) / (d*Pi) | vc = (n*d*Pi) / 1000 | d = (vc*1000) / (n*Pi) | |
Vorschubgeschwindigkeit | vf = fz*z*n | fz = vf / (z*n) | z = vf / (fz*n) | n = vf / (fz*z) |
Vorschubgeschwindigkeit | vf = n*f | n = vf / f | f = vf/n | |
Vorschub | f = fz*z | fz = f/z | z = f/fz |
Formelzeichen – Eine Übersicht der Verwendeten Formelzeichen
Beschreibung | Formelzeichen | Einheit |
Anzahl der Schneiden | Z | 1 |
Schneidkreis / Durchmesser | D | mm |
Schnittgeschwindigkeit | vc | m/min |
Drehzahl | N | 1/min oder U/min |
Vorschub pro Zahn | fz | mm |
Vorschubgeschwindigkeit | vf | mm/min |
Vorschub | f | mm/1 oder mm/U |
Formelzeichen – Eine Beschreibung der verwendeten Formelzeichen
Z – Anzahl der Schneiden
Benennt die Schneidenzahl eines Werkzeuges.
D – Schneidkreis-Durchmesser
Der Schneidkreisdurchmesser D ist der zur Schnittdatenbestimmung relevanten Durchmesser. Bei Schaftfräsern entspricht dieser dem Werkzeugdurchmesser. Stehen z.B. bei einem Werkzeug die Schneiden schräg, ist es möglich einen gemittelten Durchmesser zu wählen. Dies kann z.B. bei einem Fasenfräser Ø8 zu besseren Einsatzwerten uns somit einer höheren Standzeiten führen, wenn dieser auf einer Höhe von 1mm (einem Durchmesser von 2mm) eingesetzt wird.
vc – Schnittgeschwindigkeit
Die Schnittgeschwindigkeit ist eine von Werkzeug und Werkstückmaterial abhängige Größe. Sie drückt aus wie schnell sich die Schneide am Schneidkreisdurchmesser (durch das Material) bewegt. Die Einheit der Schnittgeschwindigkeit Vc wird in Meter pro Minute [m/min] angegeben.
N – Drehzahl
Die Drehzahl gibt an wie oft sich das Werkzeug pro Minute dreht. Die Einheit Umdrehungen pro Minute wird korrekt als 1/min geschrieben. Häufig findet man auch die Schreibweise U/min. Sie ist bei der Bearbeitung einer von zwei zentralen Einstellgrößen.
fz – Vorschub pro Zahn
Der Vorschub pro Zahn bezeichnet den Weg, den das Werkzeug pro Zahn und Umdrehung zurücklegt.
vf – Vorschubgeschwindigkeit
Die Vorschubgeschwindigkeit vf bezeichnet die Geschwindigkeit mit der das Fräswerkzeug durch das Werkstück bewegt wird. Sie hat einen Einfluss auf die Maschinenlast, den Werkzeugverschleiß, die Oberflächengüte und die Produktivität. Sie ist bei der Bearbeitung einer von zwei zentralen Einstellgrößen.
f – Vorschub
Der Vorschub gibt an wie weit sich das Werkzeug innerhalb einer Umdrehung vorwärts bewegt.
Freiformflächen Bearbeitung / 3D Fräsen
.
G
Gegenlauffräsen:
Beim Gegenlauffräsen dreht das Werkzeug entgegen der Abrollrichtung. Bearbeitet man eine Außenkontur im Gegenlauf, so verläuft die Werkzeugbahn gegen den Uhrzeigersinn. Umgekehrt bei der Bearbeitung einer Tasche im Gegenlauf, hier verläuft die Bahn im Uhrzeigersinn.
Der Vorteile ist:
– Bei harten Werkstoffen oder Oberflächenschichten ist mit weniger Werkzeugverschleiß zu rechnen als beim Gleichlauffräsen.
Die Nachteile:
– Durch die Bearbeitungskräfte wird das Werkzeug eher in die herzustellende Kontur hineingezogen. Somit ist Vorsicht geboten, damit das Fertigmaß nicht unterschritten wird.
– Schlechtere Oberfläche als beim Gleichlauffräsen.
Verwandte Glossareinträge:
Gegenlauffräsen / Gleichlauffräsen
Gewinde:
folgend finden Sie eine Auswahl an häufigen Gewinden, mit Steigung und dem zu bohrenden Kernlochdurchmesser.
Gewinde – Verwendete Kurzzeichen:
Gewindebezeichnung: Gew.
Steigung: P [mm]
Kernlochdurchmesser: KL [mm]
Gewinde – Metrische Normgewinde:
Gew. | P | KL | Gew. | P | KL | Gew. | P | KL | ||
M 1 | 0,25 | 0,75 | M 4 | 0,7 | 3,3 | M 16 | 2 | 24 | ||
M1,2 | 0,25 | 0,95 | M 5 | 0,8 | 1,2 | M 20 | 2,5 | 30 | ||
M 1,6 | 0,35 | 1,25 | M 6 | 1 | 5,0 | M 24 | 3 | 36 | ||
M 2 | 0,4 | 1,6 | M 8 | 1,25 | 13 | M 30 | 3,5 | 46 | ||
M 2,5 | 0,45 | 2,05 | M 10 | 1,5 | 16 | M 36 | 4 | 55 | ||
M 3 | 0,5 | 2,5 | M 12 | 1,75 | 18 | M 42 | 4,5 | 65 |
Gewinde – Metrische Feingewinde:
Gew. x P | KL | Gew. x P | KL | Gew. x P | KL | ||
M 2 x 0,25 | 1,75 | M 8 x 0,25 | 7,75 | M 16 x 0,5 | 15,5 | ||
M 3 x 0,25 | 2,75 | M 8 x 0,5 | 7,5 | M 16 x 1 | 15 | ||
M 4 x 0,2 | 3,8 | M 8 x 1 | 7 | M 16 x 1,5 | 14,5 | ||
M 4 x 0,35 | 3,65 | M 10 x 0,25 | 9,75 | M 20 x 1 | 19 | ||
M 5 x 0,25 | 4,75 | M 10 x 0,5 | 9,5 | M 20 x 1,5 | 18,5 | ||
M 5 x 0,5 | 4,5 | M 10 x 1 | 9 | M 24 x 1,5 | 22,5 | ||
M 6 x 0,25 | 5,75 | M 12 x 0,35 | 11,65 | M 24 x 2 | 22 | ||
M 6 x 0,5 | 5,5 | M 12 x 0,5 | 11,5 | M 30 x 1,5 | 28,5 | ||
M 6 x 0,75 | 5,25 | M 12 x 1 | 11 | M 30 x 2 | 28 |
Gewinde – Rohrgewinde / Zollgewinde:
Vergl. DIN ISO 228-1 (Nicht selbst dichtende Gewinde)
Gew. | P | KL | Gew. | P | KL | |
G1/16 | 0,907 | 6,6 | G1 | 2,309 | 30 | |
G1/8 | 0,907 | 8,6 | G1 1/4 | 2,309 | 39 | |
G1/4 | 1,337 | 11,5 | G1 1/2 | 2,309 | 45 | |
G3/8 | 1,337 | 15 | G2 | 2,309 | 57 | |
G1/2 | 1,814 | 18,5 | G2 1/2 | 2,309 | 72 | |
G3/4 | 1,814 | 24 | G3 | 2,309 | 85 |
Gewinde – UNC Gewinde:
Gew. | P | KL | Gew. | P | KL | |
1 – 64 UNC | 0,397 | 1,5 | 8 – 32 UNC | 0,794 | 3,4 | |
2 – 56 UNC | 0,453 | 1,8 | 10 – 24 UNC | 1,058 | 3,8 | |
3 – 48 UNC | 0,529 | 2,1 | 12 – 24 UNC | 1,058 | 4,5 | |
4 – 40 UNC | 0,635 | 2,3 | 1/4“ – 20 UNC | 1,270 | 5,1 | |
5 – 40 UNC | 0,635 | 2,6 | 5/16“ – 18 UNC | 1,411 | 6,6 | |
6 – 32 UNC | 0,794 | 2,8 | 3/8“ – 16 UNC | 1,587 | 8,0 |
Gleichlauffräsen:
Beim Gleichlauffräsen rollt der Fräser sinnbildlich auf der zu fräsenden Kontur ab. Bearbeitet man eine Außenkontur im Gleichlauf, so verläuft die Werkzeugbahn im Uhrzeigersinn. Umgekehrt bei der Bearbeitung einer Tasche im Gleichlauf, dann verläuft die Bahn entgegen dem Uhrzeigersinn.
Die Vorteile sind:
– Durch die Bearbeitungskräfte wird das Werkzeug eher von der Kontur weggedrückt. Somit bleibt eher ein Wandaufmaß stehen, dem man mit einem zweiten durchlauf der Bahn Rechnung tragen kann.
– Bessere Oberfläche als beim Gegenlauffräsen.
Der Nachteil:
– Bei harten Werkstoffen oder Oberflächenschichten ist mit mehr Werkzeugverschleiß zu rechnen als beim Gegenlauffräsen.
Verwandte Glossareinträge:
Gegenlauffräsen / Gleichlauffräsen
.
H
Hartanodisieren
Verwandte Glossareinträge:
Harteloxieren / Hartanodisieren
Harteloxieren
Durch Harteloxal wird eine hohe Abriebfestigkeit, Verschleißfestigkeit, Härte und Korrosionsbeständigkeit hergestellt.
Die Farbe von Harteloxal:
- Die Eigenfarbe von Harteloxal kann von Grau über Braun bis hin zu Schwarz variieren.
Generell besitzen Hartanodisierschichten eine charakteristische Farbe, welche von der Zusammensetzung der Legierung des Grundmaterials abhängt. Unterschiedliche Legierungsbestandteile wie Silizium, Kupfer, Mangan und Zink können zu einer Trübung und Färbung der Oxidschicht führen. - Zulässige Schwankungen der Legierungsbestandteile einer bestimmten Legierung können bei verschiedenen Rohmaterialchargen und gleicher Schichtdicke eine Farbveränderung verursachen.
- Die Farbe des Bauteils wird mit steigender Schichtdicke dunkler.
Für Sichtbauteile kann die Eloxalschicht schwarz eingefärbt werden. Dies führt zu einer konstanten Farbgebung und somit zu einem stabilen Prozess. Zuvor beschriebene Störgrößen hinsichtlich einer konstanten Farbe werden so umgangen.
Verwandte Glossareinträge:
Harteloxieren / Hartanodisieren
Härteverzug
Hartfräsen
Beim Hartfräsen werden gehärtete Stähle zerspant. Herkömmlich kennt man für diese Aufgaben die Fertigungsverfahren Senkerodieren, Drahtschneiden, Flach– oder Diaformschleifen. Jedes dieser Verfahren hat seine eigenen Vorzüge und Nachteile.
Hartfräsen ist hier eine sehr flexible und wirtschaftliche Ergänzung, bei gleichzeitig guter Maßhaltigkeit und Oberflächengüte.
Je nach der Bearbeitungsaufgabe empfehlen sich andere Werkzeugformen. So sind zum Beispiel Hoch-Vorschub-Wendeschneidplattenwerkzeuge für Ebene Bereiche interessant. Für Senkrechte Wände können geeignete Schaftfräser verwendet werden. In der 3D Bearbeitung können für steile Bereiche Tonnenfräser für flache Torusfräser herangezogen werden.
Unabhängig vom Werkzeugtyp ist eine kleine Zustellung und ein hoher Vorschub anzustreben.
Verwandte Glossareinträge:
Hartfräsen / HSC Cutting / HPC Cutting
HPC Cutting – High Performance Cutting
Beim HPC Fräsen wird mit geeigneten Werkzeugen, normal dynamischen Maschinen und intelligenten Bearbeitungsstrategien (Trochodialen Werkzeugbahnen, Spiralisierten Werkzeugbahnen, …) eins sehr hohes Zeit-Span-Volumen erzeugt.
Verwandte Glossareinträge:
Hartfräsen / HSC Cutting / HPC Cutting
HSC Cutting – High Speed Cutting
Beim Hochgeschwindigkeitsfräsen wird mit sehr hohen Schnittgeschwindigkeiten, Vorschüben und geringen Zustellungen gearbeitet. Vorteile dieses Verfahrens sind:
– Reduzierte Schnittkräfte
– Reduzierter Verschleiß
– Die Bearbeitung dünnwandiger Bauteile wird vereinfacht
– Die Bearbeitung harter Bauteile wird möglich
– Erhöhtes Zeitspanvolumen
Zu beachten ist, dass HSC- Fräsmaschinen hochdynamisch sind, die Spindeln sehr hohe Drehzahlen realisieren können, jedoch nur ein sehr geringes Drehmoment aufweisen. Dies erfordert z.T. andere Werkzeuge als die z.B. bei Universalfräsmaschinen üblichen.
Verwandte Glossareinträge:
Hartfräsen / HSC Cutting / HPC Cutting
.
I
Induktionshärten / Induktiv Härten
Beim Induktionshärten wird der Stahl durch eine Spule umschlossen. Diese wird mit Wechselstrom beaufschlagt und erzeugt somit ein oszillierendes Magnetfeld. Dadurch werden Wirbelströme im Material induziert, welche durch den inneren Wiederstand des Materials die gewünschte Temperatur erzeugen.
Mit etwas Abstand zur Spuhle sitzen Wasserdüsen, die das Werkstück Abschrecken um das gewünschte Gefüge / die gewünschte Härte zu erzeugen.
Der Vorteil des Induktionshärten ist, dass so auch nur Teile eines Werkstücks gehärtet werden können. Entgegen dem Härten im Ofen ist hier jedoch ein erhöhter Rüstaufwand erforderlich, was sich in höheren Kosten niederschlägt.
Verwandte Glossareinträge:
Randschichthärten
M
Materialzeugnis: Werksbescheinigung 2.1 nach EN 10204
- Mit der Bescheinigung wird die Übereinstimmung mit der Bestellung bestätigt
- Die Ausstellung der Bescheinigung erfolgt durch den Hersteller
Verwandte Seiteninhalte:
Qualitätssicherung Materialprüfzeugnis
Verwandte Glossareinträge:
Werkszeugnis 2.2 nach EN 10204 / Abnahmeprüfzeugnis 3.1 nach EN 10204 / FDA Zulassung
Materialzeugnis: Werkszeugnis 2.2 nach EN 10204
- Mit der Bescheinigung wird die Übereinstimmung mit der Bestellung bestätigt
- Die Ausstellung der Bescheinigung erfolgt durch den Hersteller
- Es werden Ergebnisse nicht spezifizierter Prüfungen ausgewiesen
Verwandte Seiteninhalte:
Qualitätssicherung Materialprüfzeugnis
Verwandte Glossareinträge:
Werksbescheinigung 2.1 nach EN 10204 / Abnahmeprüfzeugnis 3.1 nach EN 10204 / FDA Zulassung
Materialzeugnis: Abnahmeprüfzeugnis 3.1 nach EN 10204
- Mit der Bescheinigung wird die Übereinstimmung mit der Bestellung bestätigt
- Die Ausstellung der Bescheinigung erfolgt durch einen fertigungsunabhängigen Abnahmebeauftragten des Herstellers
- Es werden Ergebnisse spezifizierter Prüfungen ausgewiesen
Verwandte Seiteninhalte:
Qualitätssicherung Materialprüfzeugnis
Verwandte Glossareinträge:
Werksbescheinigung 2.1 nach EN 10204 / Werkszeugnis 2.2 nach EN 10204 / FDA Zulassung
Materialzeugnis: FDA
Bestätigung der Zulassung des Materials durch die US- Amerikanische Behörde Food ans Drug Administration (FDA).
Verwandte Seiteninhalte:
Qualitätssicherung Materialprüfzeugnis
Verwandte Glossareinträge:
Werksbescheinigung 2.1 nach EN 10204 / Werkszeugnis 2.2 nach EN 10204 / Abnahmeprüfzeugnis 3.1 nach EN 10204
N
Nitrieren
Dieses Verfahren ist eine Wärmebehandlung und hat das Ziel, die Oberflächenhärte sowie die Verschleißfestigkeit von Stahlteilen zu erhöhen. Besonders bei beanspruchten Bauteilen wird das Nitrieren häufig angewendet. Eine nachfolgende Brünierung, welche dem Bauteil eine schwarze Färbung verleiht, bietet nicht nur einen optischen Mehrwert, sondern verbessert auch den Korrosionsschutz. Es gibt verschiedene Nitrierverfahren, zu den gängigsten gehören:
- Kurzzeitnitrieren / Kurzzeit Gasnitrieren / KZN
Die Bezeichnung Kurzzeitnitrieren bezieht sich auf die Dauer der Wärmebehandlung. Es ist ein relativ schnelles Verfahren um die Oberflächenhärte zu erhöhen. Der Begriff ist nicht fest definiert. Daraus folgt, dass bei Verwendung des Begriffes kein Anspruch auf eine definierte Schichtdicke besteht. Eine gängige Schichtdicke des Kurzzeitnitrierens ist 0,3mm.
- Langzeitnitrieren / Langzeit Gasnitrieren / LZN
Analoges gilt für das Langzeitnitrieren, mit einer stark erhöhten Durchlaufzeit und gängigen Schichtdicke von 0,6mm.
- Plasmanitrieren
Vorteile des Nitrierens:
- Kosteneffizienz:
Das Verfahren ist relativ günstig. - Prozessoptimierung:
Das Bauteil wird zuerst komplett gefertigt und anschließend nitriert. Dies minimiert die benötigten Fertigungsprozesse und reduziert die Durchlaufzeit. - Oberflächenhärte:
Die Härte der Nitrierschicht hängt vom verwendeten Werkstoff ab. - Geringer Verzug:
Das Verfahren verursacht nur minimalen Verzug am Bauteil.
Nachteile des Nitrierens:
- Passmaße:
Abhängig von den Toleranzanforderungen kann es erforderlich sein, bei Passungen die Maßänderungen durch das nitrieren Abzuschätzen und zu berücksichtigen. - Verzug bei engen Passungen:
Selbst ein minimaler Verzug kann bei engen Toleranzen problematisch sein, wodurch sich sehr enge Passungen nicht prozesssicher herstellen lassen. Dies kann eine nachträgliche Bearbeitung notwendig machen. - Nacharbeit:
Ist ein Passmaß nach dem Nitrieren nicht mehr Maßhaltig, wird eine Nacharbeit erforderlich. Dies erfolgt beispielsweise durch Aufreiben oder Schleifen von Passbohrungen und anderen Flächen. Dadurch wird die Nitrierschicht rasch abgetragen, wodurch es zu einem Härteverlust kommen kann. Als Lösung kann bei einer Neufertigung ein anderer Werkstoff gewählt und das Bauteil gehärtet und ggf. anschließend geschliffen und/oder erodiert werden.
P
Polieren
Beim polieren wird mit Polierpaste und einem Werkzeug (z.B. einem Polierstift, einer Polierscheibe, einer Polierbürste oder einem Polierfächer) die Rauheit einer Fläche verringert. Dies geschieht zum Teil durch Materialabtrag und durch Kaltumformung. Scharfe Anteile der Polierpaste tragen Material ab, nicht schneidende Anteile rollen über Oberfläche und glätten die vorhandenen Spitzen. Je nach zu erreichender Oberfläche variieren im Poliermittel die Anteile runder und schneidender Körner sowie deren Korngröße.
Zielsetzung beim Polieren kann sein:
– die Reduzierung von Reibung (Temperatur, Verschleiß, Kraft, …)
– das vermindern von anhaftendem Fremdmaterial
– das Herstellen von optischen Eigenschaften der Oberfläche
Voraussetzung zum Polieren:
Das Material muss polierbar sein.
Die Rauheit der Fläche muss vor dem Polieren ausreichend gering sein.
Einfluss auf Toleranzen:
Der vorhandene Materialabtrag muss bei feinsten Maß-, Form und Lagetoleranzen berücksichtigt werden.
Verwandte Seitenbereiche:
Zusatzleistungen – polieren
S
Schnittgrößen:
Als Schnittgrößen, werden die Größen genannt, die direkt über das Programm / durch den Bediener vorgegeben werden. Dazu gehören die Drehzahl des Werkzeuges, die Vorschubgeschwindigkeit, die Eingriffsbreite und die Schnitttiefe.
Verwandte Glossareinträge:
Eingriffsbreite ae / Formeln Fräsen ff./ Schnittgrößen / Schnitttiefe ap
Schnitttiefe ap:
Die Schnitttiefe ap beschreibt im Regelfall die Zustellung entlang der Werkzeugachse.
Sowohl die Eingriffsbreite ae als auch die Schnitttiefe ap hängen vom Werkzeugtyp und dem Material des Werkstücks ab. Für spezifische Einsatzwerte kann man sich auf Tabellen der Werkzeughersteller beziehen.
Die richtige Einstellung dieser Parameter hat direkte Auswirkungen auf die Belastung und den Verschleiß des Werkzeugs. Durch die Optimierung der Eingriffsbreite und Schnitttiefe können nicht nur die Lebensdauer des Werkzeugs verlängert und die Bearbeitungszeit verkürzt werden, sondern auch die Qualität der bearbeiteten Oberfläche und die Maßhaltigkeit verbessert werden. Zudem führt dies zu einem stabileren Fräsprozess.
ap und ae bei einem Schaftfräser:
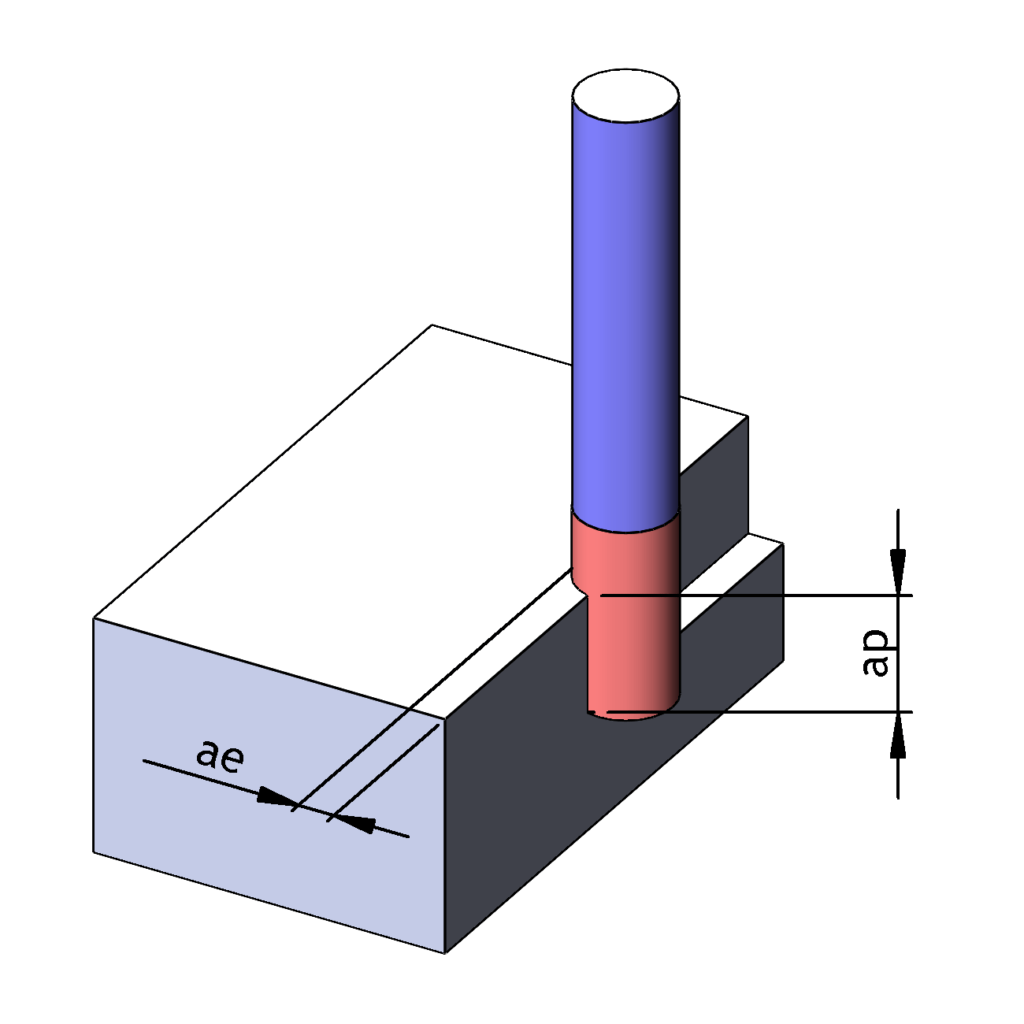
ap und ae bei einem Messerkopf:
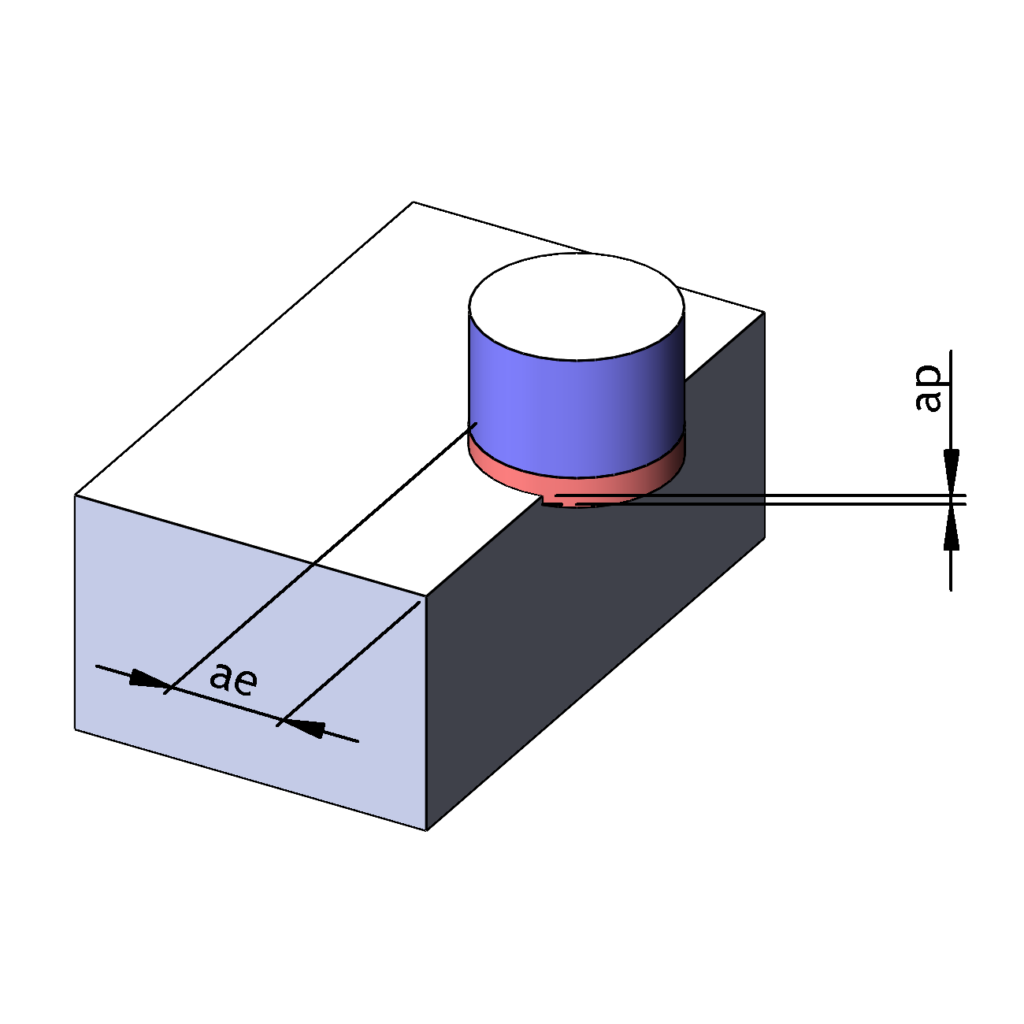
Verwandte Glossareinträge:
Eingriffsbreite ae / Formeln Fräsen ff./ Schnittgrößen / Schnitttiefe ap
Senkungen für Schrauben DIN 912 / ISO 4762 (mit Zylinderkopf)
Verwendete Kurzzeichen:
d – Bohrungsdurchmesser
D – Senkdurchmesser
T – Senktiefe
Gewinde | d | D | T |
M3 | 3,4 | 6,5 | 3,4 |
M4 | 4,5 | 8 | 4,4 |
M5 | 5,5 | 10 | 5,4 |
M6 | 6,6 | 11 | 6,4 |
M8 | 9 | 15 | 8,6 |
M10 | 11 | 18 | 10,6 |
M12 | 13,5 | 20 | 12,6 |
M16 | 17,5 | 26 | 16,6 |
M20 | 22 | 33 | 20,6 |
Senkungen für Schrauben DIN 7991 / ISO 10642 (mit Senkkopf)
Für alle Senkungen:
90° Spitzenwinkel des Senkers
Verwendete Kurzzeichen:
d – Bohrungsdurchmesser
D – Senkdurchmesser
Gewinde | d | D |
M3 | 3,4 | 6,9 |
M4 | 4,5 | 9,2 |
M5 | 5,5 | 11,5 |
M6 | 6,6 | 13,7 |
M8 | 9 | 18,3 |
M10 | 11 | 22,7 |
M12 | 13,5 | 27,2 |
Stirnfräsen / Stirnen / Planfräsen:
Beim Stirnfräsen ist die Eingriffsbreite ae gewöhnlich deutlich größer als die Schnitttiefe ap. Die bearbeitete Fläche steht im Regelfall 90° zur Werkzeugachse.
Verwandte Glossareinträge:
Stirnfräsen / Vollnutfräsen / Walzfräßen
V
Vakuumhärten
Vergütungsstähle
Stähle der Gruppe Vergütungsstähle erhalten durch das Vergüten eine hohe Zug- und Dauerfestigkeit.
Vergüten nennt man das härten und anschließendes anlassen von Stählen.
Für dieses Verfahren sind zum Beispiel folgende Stähle geeignet:
C45 / C50 / C55 / C60
Vollnutfräsen:
Beim Vollnutfräsen erzeugt die Fräsbahn eine beidseitige Wand neben dem Werkzeug. Der Umschlingungswinkel ist 180°. Die Eingriffsbreite ae ist gleich dem Werkzeugdurchmesser. Die Schnitttiefe ap ist gewöhnlich größer 0,5 mal dem Werkzeugdurchmesser.
Der Gleichlaufanteil der Fräskräfte drückt den Fräser weg. Der Gegenlaufanteil der Fräskräfte zieht an dem Fräser. Beide Effekte addieren sich und es kommt beim Einsatz von Schaftfräsern zu einer relevanten Verformung des Werkzeuges. Diese zeigt sich bei pendelnder Zustellung durch Absätzen an den Nutwänden.
Verwandte Glossareinträge:
Stirnfräsen / Vollnutfräsen / Walzfräßen
Vorschubberechnung beim Fräsen
Formeln zur Vorschubberechnung beim Fräsen finden Sie [hier]
W
Walzfräsen:
Beim Walzfräsen ist die Schnitttiefe ap gewöhnlich deutlich größer als die Eingriffsbreite ae. Die bearbeitete Fläche steht im Regelfall 90° zur Werkzeugachse.
Verwandte Glossareinträge:
Stirnfräsen / Vollnutfräsen / Walzfräsen
Werksbescheinigung (Kontext Material):
den entsprechenden Glossareintrag finden Sie [hier].
Verwandte Glossareinträge:
2.1 – Werksbescheinigung / 2.2 – Werkszeugnis / 3.1 – Abnahmeprüfzeugnis / FDA Zulassung
Werkszeugnis (Kontext Material):
den entsprechenden Glossareintrag finden Sie [hier].
Verwandte Glossareinträge:
2.1 – Werksbescheinigung / 2.2 – Werkszeugnis / 3.1 – Abnahmeprüfzeugnis / FDA Zulassung